Looking Good Info About What Is The Color Code For 3-phase

Understanding 3-Phase Color Codes
1. Why Color Codes Matter
Ever wondered why electrical wires aren't just a jumbled mess of silver strands? It's all thanks to color codes! These codes are a standardized system that helps electricians and technicians quickly identify the purpose of each wire within a circuit. When it comes to three-phase power systems, these color codes become absolutely crucial for safety and proper functioning. Imagine trying to troubleshoot a complex motor control system without knowing which wire does what! A properly implemented color code system prevents mistakes, streamlines maintenance, and most importantly, keeps everyone safe. Think of it like a secret language spoken through colored insulation.
Think about assembling furniture without instructions — chaotic, right? Electrical work without color codes is similar. It's not just about identifying phases; it's about avoiding potentially disastrous scenarios. Improper wiring in a three-phase system can lead to equipment damage, power outages, and even electrical shocks. These codes act as a visual guide, ensuring that the system is wired correctly and that each phase is properly aligned. This minimizes the risk of imbalance, which is a major headache in three-phase systems.
The whole point of using standardized color codes boils down to improving communication and reducing errors. It's an internationally recognized system that allows electricians from different backgrounds to work together seamlessly. Whether you're in a factory, a commercial building, or a data center, the colors provide a common language for understanding the electrical system. This standardization facilitates quicker troubleshooting, faster repairs, and ultimately, a more efficient and safer electrical environment. It's a simple concept with a huge impact.
But are these color codes always the same? Not exactly. There are different standards used in different regions around the world. North America (following the NEC or National Electrical Code) has one set of colors, while Europe (following IEC standards) uses another. Knowing which standard applies to your particular project is vital. Using the wrong colors can lead to confusion, delays, and potentially dangerous situations. It's like ordering pizza with the wrong toppings — technically still pizza, but definitely not what you expected.
North American Color Codes (NEC)
2. The NEC Standard
If you're working with electrical systems in North America, then the National Electrical Code (NEC) is your bible. The NEC specifies the color codes for three-phase systems, and sticking to these guidelines is non-negotiable. It's not just a suggestion; it's the law (or at least, heavily enforced regulations!). Ignoring these codes could result in fines, project delays, and, more seriously, safety hazards. So, let's dive into the specifics for identifying each phase.
In a 480Y/277V three-phase system, the most common voltage level for commercial and industrial applications, the color code is as follows: Phase A is typically brown, Phase B is orange, and Phase C is yellow. A neutral conductor, if present, is always white or gray. The ground wire is green or green with a yellow stripe. These colors are your visual roadmap to navigating the electrical system. Imagine each color shouting out its purpose, making it easier to differentiate each component.
Now, what about a 208Y/120V system? This is another very common voltage level often found in office buildings and light industrial settings. Here, the color code changes slightly: Phase A is black, Phase B is red, and Phase C is blue. Again, the neutral conductor remains white or gray, and the ground wire stays green or green with a yellow stripe. Notice how the colors shift to accommodate the different voltage level. This prevents confusion and helps maintain the integrity of the system.
It's crucial to remember that these color codes apply primarily to the conductors or wires themselves. The conduit (the pipe that holds the wires) is usually a different color — often gray or metallic. This helps to distinguish between the wiring and the enclosure it runs through. Also, be aware that there might be variations or exceptions depending on the specific jurisdiction or facility. Always double-check local regulations and company policies before starting any electrical work. Better safe than sorry, right?
Mountain Warehouse Mens Phase Extreme Waterproof Ski Jacket Fashion
European Color Codes (IEC)
3. The IEC Standard
Across the pond, in Europe and other regions that follow the International Electrotechnical Commission (IEC) standards, the color coding is different. If you're working on projects that adhere to IEC, it's essential to switch gears and familiarize yourself with their system. Mixing up IEC and NEC color codes is a recipe for disaster, and could lead to major misconnections and potential accidents. So let's get the straight story on IEC wiring colors.
Under the IEC standard, the color codes for a three-phase system are typically as follows: Phase L1 is brown, Phase L2 is black, and Phase L3 is gray. The neutral conductor, just like in North America, is usually blue. And again, the protective earth (ground) is green and yellow striped. This system is quite different from the North American setup, particularly in how phases B and C are indicated.
It is vital to remember that older IEC installations may still use red, yellow, and blue for the phases. However, the modern standard is brown, black, and gray. This can add another layer of complexity, particularly when working on existing systems. A careful review of the system documentation and a thorough inspection are essential to avoid confusion.
One significant point to remember is that the color blue is exclusively reserved for the neutral conductor under IEC standards. This is a key distinction from the North American system, where blue can sometimes be used for a phase conductor in a 208Y/120V system. Using blue for anything other than neutral in an IEC system is a major no-no and can lead to dangerous situations. So, double-check those blues!

Why Consistency is King
4. The Ripple Effect of Incorrect Color Coding
Imagine a scenario where a new electrician, unfamiliar with the facility's idiosyncratic wiring, needs to replace a faulty motor. They assume the colors follow the standard convention, but they don't. Chaos ensues. The motor spins in the wrong direction, potentially damaging connected equipment. This seemingly small error has triggered a cascade of problems. This is the reality of what can happen when color coding is not consistently applied and followed.
Consistent color coding simplifies maintenance and troubleshooting. When everyone adheres to the same standards, it's much easier to identify the source of a problem. Instead of spending hours tracing wires, an electrician can quickly pinpoint the phase that's causing the issue. This saves time, reduces downtime, and ultimately, saves money. Think of it as having a well-organized toolbox — you can find exactly what you need when you need it.
Moreover, consistent color coding enhances safety. It minimizes the risk of accidental contact with live wires. If everyone knows that, for example, brown always represents a specific phase, they can take appropriate precautions. This is especially important when working on high-voltage systems, where the consequences of a mistake can be severe. It's a simple yet effective way to protect workers and prevent accidents.
To ensure consistency, organizations should develop and implement clear color-coding policies. These policies should outline the specific colors used for each type of conductor, as well as the procedures for labeling and documenting the wiring. Regular training and audits can help to reinforce these policies and ensure that everyone is following the rules. Its like having a rulebook for electricity; everyone needs to be on the same page.
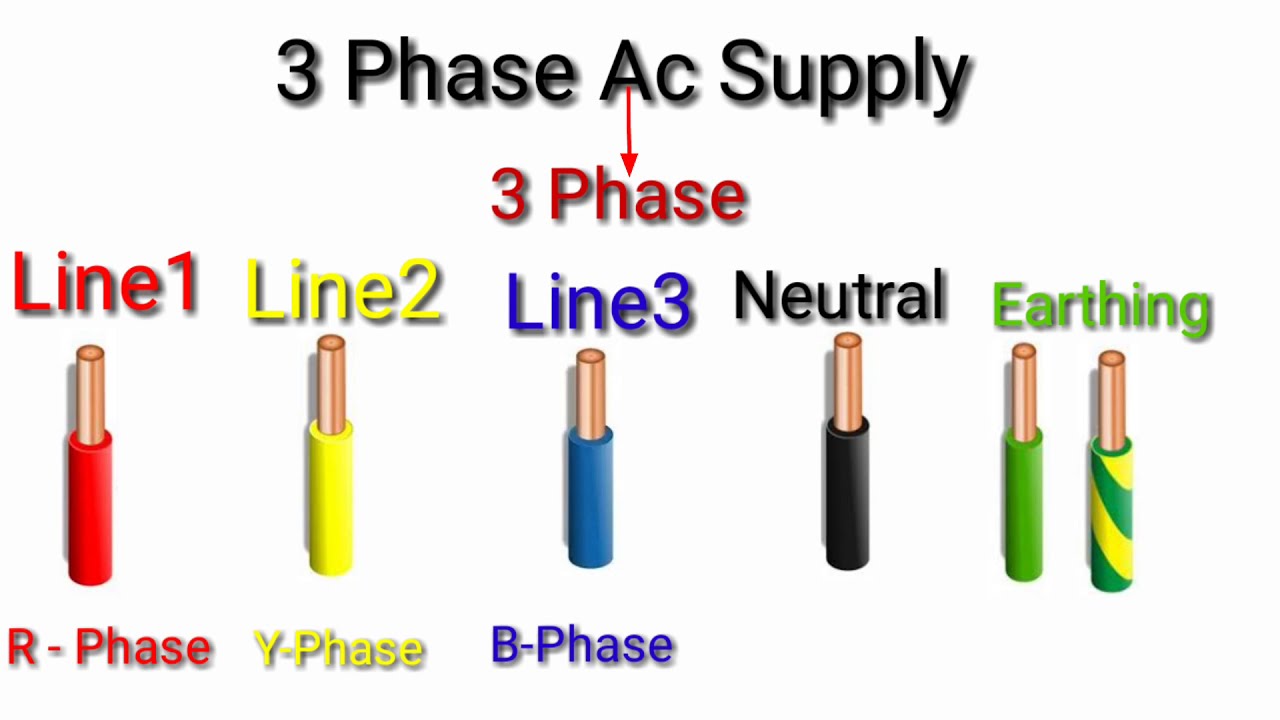
Electrical Wiring Color Codes For AC DC NEC IEC, 43 OFF
Practical Tips and Best Practices
5. Making Color Codes Work for You
So, how can you ensure you're always on top of your color-coding game? First, always consult the relevant electrical codes and standards for your region or project. Whether it's the NEC in North America or the IEC in Europe, understanding the specific requirements is paramount. It's your responsibility to stay informed and up-to-date with the latest regulations.
Next, use appropriate labeling techniques to clearly identify conductors. Wire markers, labels, and tags can provide an extra layer of clarity, especially in complex systems. Make sure the labels are durable and resistant to harsh environments. You don't want them fading or falling off over time. It's like adding subtitles to a movie, making sure the meaning is clear even when things get noisy.
When working on existing systems, take the time to verify the color coding before making any changes. Don't assume that the wiring is correct. Use a multimeter to test the voltage and identify the phases. This can prevent potentially dangerous misconnections. Always treat electrical systems with respect and double-check your work. Think of it as verifying your calculations before launching a rocket a little extra caution goes a long way.
Finally, invest in high-quality tools and materials. Using the right tools can make the job easier and safer. Color-coded wire strippers, for example, can help you avoid damaging the insulation when stripping wires. And always use wires and cables that meet the required safety standards. Cutting corners can lead to problems down the road. It's like using the right ingredients when baking a cake — quality in, quality out.

FAQ
6. Answers to Your Burning Questions
Okay, let's tackle some frequently asked questions about color codes in three-phase electrical systems. Sometimes, the theory is clear, but the real-world application brings up some unexpected scenarios. So, let's clear up some common points of confusion.
Q: What happens if the color of the wire I need isn't available?
A: If you can't find the exact color-coded wire you need, you can use white or gray wire and mark it with colored tape or heat-shrink tubing at each termination point. Make sure the marking is clear, durable, and visible. The key is to ensure that the color coding is easily identifiable, even if the wire itself isn't the correct color. It's kind of like wearing a costume — you might not be the superhero, but you sure look like one!
Q: Can I use any color I want for my three-phase system, as long as I'm consistent?
A: Absolutely not! Adhering to the established color codes (NEC or IEC, depending on your location) is crucial for safety and compliance. Deviating from these standards can lead to confusion, misconnections, and potentially hazardous situations. It's like trying to drive on the wrong side of the road — it might work for a little while, but it's bound to end badly.
Q: What do I do if I encounter an older system with non-standard color coding?
A: If you're working on an older system with non-standard color coding, proceed with caution. Carefully trace and identify each conductor before making any changes. Use a multimeter to verify the voltage and phase. Document your findings and label the wires clearly. Consider bringing the system up to current standards if possible. It's like archaeology — carefully uncovering the past and trying to make sense of it, while ensuring future safety.