Painstaking Lessons Of Info About What Is The Best Method For Splicing Wires

Splice Wire Groslift
Splicing Wires
So, you're diving into the world of electrical work, huh? Or maybe you just need to fix that pesky lamp that's been flickering for months. Either way, at some point, you're going to need to splice some wires. Now, before you go twisting wires together like you're making friendship bracelets, let's talk about the best way to do it. Because let's be honest, a shoddy splice can lead to everything from a minor inconvenience to a full-blown electrical fire. And nobody wants that!
The phrase "best method" is a loaded one. It really depends on the situation. Are we talking about splicing wires in a junction box? Inside a car? Outdoors? Each environment has its own set of considerations. But don't worry, we'll cover the most common scenarios and the techniques that'll keep your connections safe and reliable. This is one of those things where a little knowledge goes a long way.
Think of it this way: properly splicing wires is like making a good cup of coffee. You could just throw some grounds in hot water and call it a day, but taking the time to do it right yields a much better result. Similarly, taking the time to learn the proper techniques for splicing wires will give you peace of mind knowing that your electrical connections are solid and safe.
Remember that electricity can be dangerous. If you're not comfortable working with electricity, please call a qualified electrician. Seriously. It's better to be safe than sorry (and possibly electrocuted!). But if you're confident and ready to learn, let's get splicing!
1. Understanding the Basics
Before we jump into specific methods, let's quickly cover the fundamentals of a good wire splice. What exactly are we aiming for? Well, ideally, a good splice should be electrically sound, mechanically strong, and properly insulated. Think of it as the trifecta of electrical connections.
Electrically sound means the connection should conduct electricity as efficiently as possible, with minimal resistance. A loose or poorly made connection creates resistance, which generates heat. And heat is the enemy! It can melt insulation, cause corrosion, and eventually lead to a failure. That's why a tight, secure connection is paramount.
Mechanically strong means the connection should be able to withstand physical stress and vibration without coming apart. Imagine a wire splice inside a car door that's constantly being slammed. If the splice isn't strong, it'll eventually loosen or break. This is where proper techniques and materials come into play.
Properly insulated means the bare wires are completely covered with an insulating material, such as electrical tape or a wire connector. This prevents short circuits and protects you from electrical shock. Never, ever leave bare wires exposed. It's a recipe for disaster!

The Contenders
Alright, let's get to the good stuff! Here are some of the most common and effective methods for splicing wires, each with its own pros and cons. We'll explore the pros and cons, so you can choose what works for you.
2. Wire Connectors (a.k.a. Wire Nuts)
These little plastic caps are probably the most widely used method for splicing wires in residential applications. They're easy to use, relatively inexpensive, and provide a secure and insulated connection. You simply strip the ends of the wires, twist them together (usually with pliers), and then screw the wire connector onto the twisted wires.
The key to a good wire nut connection is to make sure the wires are twisted tightly and that the wire connector is properly sized for the number and gauge of wires you're connecting. Too few twists, and the connection might be loose. Too many twists, and you might damage the wires. Also, make sure to use the right size of wire connector. Overstuffing it, or using one that's too small, can be dangerous.
Wire connectors are great for splicing solid or stranded wires, but they're not ideal for splicing wires of significantly different gauges. Also, they're generally not recommended for use in harsh environments, such as those exposed to moisture or vibration. I usually give a little tug to each wire after securing it with a wire nut to ensure it won't slip out.
Always turn the power off before working with wire nuts. It's a simple safety measure that can save you from getting shocked. Even though they are easy to use, don't get complacent and skip on safety. Trust me; those few minutes of prep time are way better than a trip to the hospital.
3. Crimp Connectors
Crimp connectors are another popular option, especially in automotive and marine applications. They provide a strong and reliable connection that's resistant to vibration and moisture. There's a wide variety of crimp connectors available, including butt connectors, ring terminals, and spade terminals. The key is to use the correct crimping tool for the type of connector you're using.
To use a crimp connector, you simply insert the stripped wires into the connector and then crimp it down tightly with the crimping tool. The crimping tool compresses the connector, creating a secure electrical and mechanical connection. I would always suggest getting a good crimping tool that offers ratcheting action; it's worth the extra money.
One of the advantages of crimp connectors is that they can be used to splice wires of different gauges. For example, you can use a butt connector to splice a 14-gauge wire to a 12-gauge wire. However, it's important to choose the correct size of connector for the wires you're splicing. Also, ensure that the crimp is tight and secure. A loose crimp can lead to the same problems as a loose wire nut connection: resistance, heat, and eventual failure.
When using crimp connectors in wet environments, make sure to use waterproof connectors. These connectors have a sealant inside that prevents moisture from entering the connection. If you're not using waterproof connectors, you can wrap the connection with heat-shrink tubing to protect it from moisture. Always double-check your work! Better safe than sorry, especially in a potentially dangerous electrical job.
4. Soldering
Soldering is a more advanced method of splicing wires that creates a very strong and reliable connection. It involves melting solder (a metal alloy) onto the wires to create a permanent bond. Soldering is often used in electronics and other applications where a high-quality connection is essential. However, it requires some skill and practice to do it properly.
To solder wires, you first need to strip and twist them together. Then, you heat the wires with a soldering iron and apply solder to the joint. The solder melts and flows into the joint, creating a strong electrical and mechanical connection. After the solder cools and solidifies, you need to insulate the joint with electrical tape or heat-shrink tubing. This prevents short circuits and protects the connection from the elements.
One of the advantages of soldering is that it creates a very low-resistance connection, which is ideal for sensitive electronic circuits. However, soldering can be time-consuming and requires specialized equipment. Also, it's important to avoid overheating the wires, as this can damage the insulation. With a little practice, though, you can become proficient and produce professional-quality solder joints.
If you choose to solder, use rosin-core solder. Do not use acid-core solder, which is designed for plumbing and can corrode electrical connections. Also, be sure to work in a well-ventilated area, as the fumes from soldering can be harmful. You've got this!
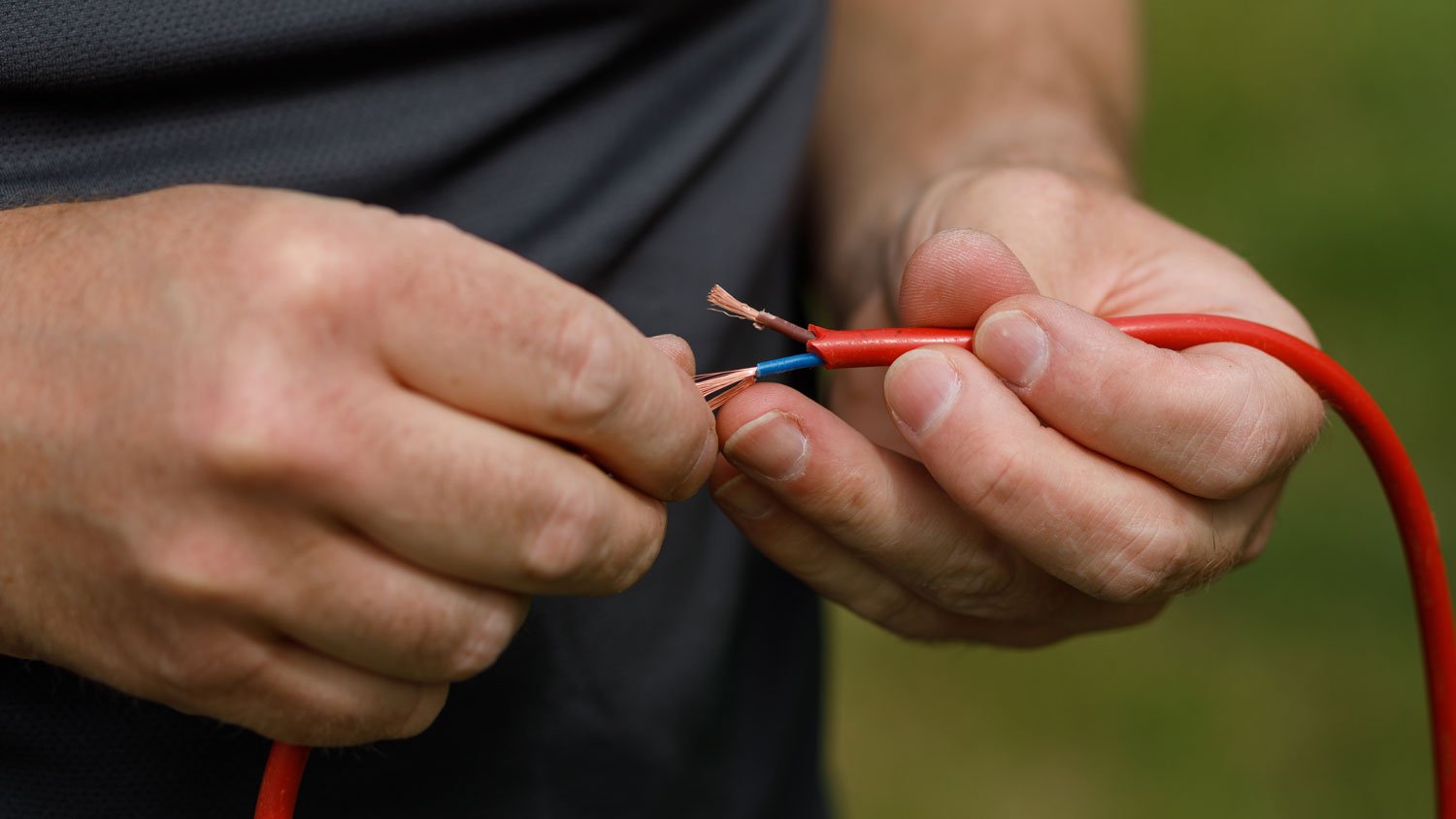
Choosing the Right Method
5. Environment and Application
As we touched on earlier, the best method for splicing wires depends on the specific environment and application. In a dry, indoor environment, wire connectors are often the most convenient and cost-effective option. However, in a wet or corrosive environment, crimp connectors or soldered connections are generally a better choice.
For example, if you're splicing wires in a car, you'll want to use crimp connectors that are designed to withstand vibration and moisture. Similarly, if you're splicing wires outdoors, you'll want to use waterproof connectors or protect the connections with heat-shrink tubing. Also consider the specific application. Are you splicing wires in a lighting circuit? Or a high-current appliance circuit? The current rating of the wires and connectors needs to be appropriate for the application.
If you're not sure which method is best for your specific situation, it's always a good idea to consult with a qualified electrician. They can assess the environment, the application, and the relevant codes and regulations to help you choose the right splicing method. I'd suggest they probably have dealt with a similar problem to yours, that's always good.
Remember, the goal is to create a safe and reliable electrical connection that will last for years to come. So take the time to choose the right method and do the job properly. Your safety and the safety of your home or vehicle depend on it.
6. Wire Type and Gauge
Another important factor to consider is the type and gauge of the wires you're splicing. Some splicing methods are better suited for solid wires, while others are better suited for stranded wires. Similarly, some methods are better for splicing wires of the same gauge, while others can accommodate wires of different gauges.
For example, wire connectors are generally suitable for splicing both solid and stranded wires of the same gauge. However, crimp connectors offer a wider range of options for splicing wires of different gauges. Soldering is also a versatile method that can be used to splice wires of different types and gauges, but it requires more skill and experience.
It's essential to choose the right splicing method and the right size of connector for the specific wires you're working with. Using the wrong method or the wrong size of connector can lead to a weak or unreliable connection. So, check the wire gauge and type before you start splicing.
Before you start, double check that everything matches up. Making the correct decision from the start can save you time and a lot of trouble later down the line. It's an essential, though often overlooked, step that'll pay off in the long run.
7. Skill Level and Tools Available
Finally, consider your own skill level and the tools that you have available. If you're a beginner, wire connectors are probably the easiest and most straightforward option. They require minimal tools and no special skills. However, if you're more experienced and have the necessary tools, crimp connectors or soldering can provide a more reliable and durable connection.
Soldering requires a soldering iron, solder, and some basic soldering skills. Crimp connectors require a crimping tool and the appropriate connectors. If you're not comfortable using these tools, it's best to stick with wire connectors or seek help from a qualified electrician. Also, don't forget about safety! Always wear safety glasses when working with electrical wires and tools. And never work on live circuits.
Ultimately, the best method for splicing wires is the one that you're most comfortable and confident using, and that meets the specific requirements of the application. So, don't be afraid to experiment and try different methods until you find the one that works best for you. Over time, you'll develop your own preferences and techniques. Don't feel like you need to master every method right now.
Assess your skills and resources to make an informed decision. By considering your proficiency and the tools at your disposal, you can pick a method you'll be comfortable with, resulting in a safe, high-quality splice.
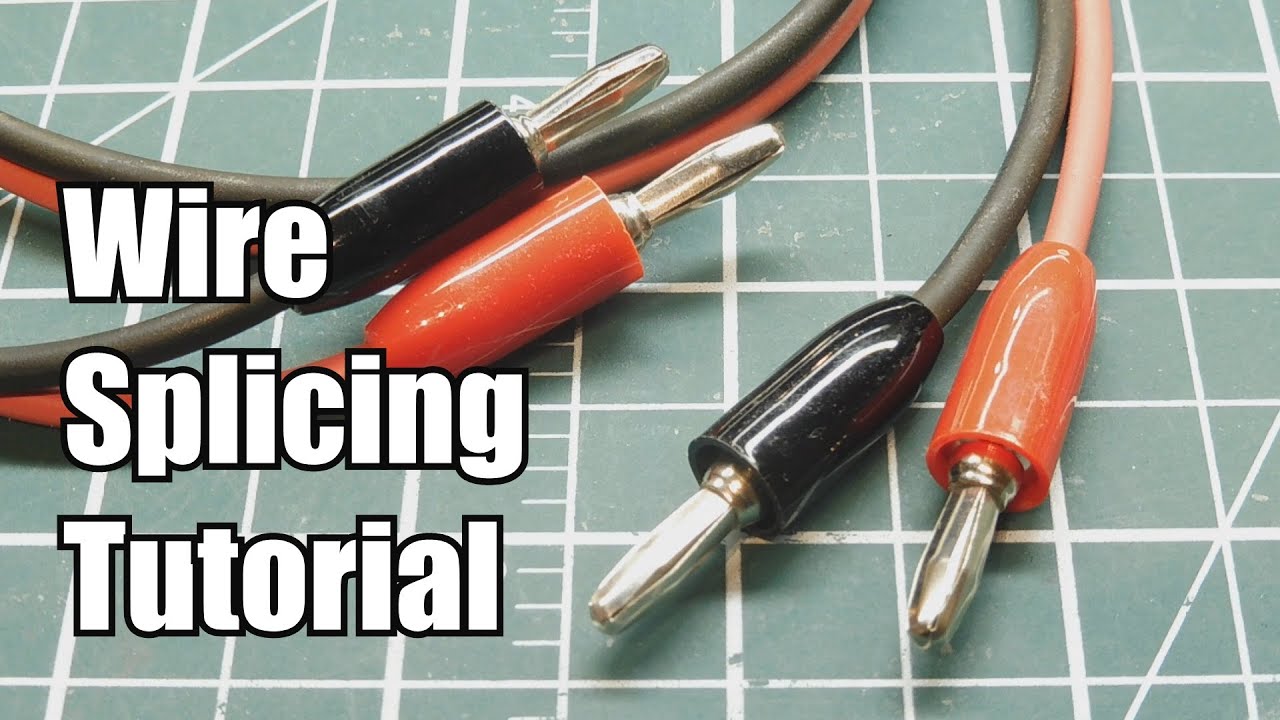
Best Practices for a Safe and Reliable Splice
8. Proper Wire Stripping
Proper wire stripping is absolutely crucial for creating a good splice. When you strip the insulation off the end of a wire, you want to remove just enough insulation to expose the bare wire without nicking or damaging the wire itself. A nicked wire is a weakened wire, and it's more likely to break under stress.
Use a wire stripper that's specifically designed for the gauge of wire you're working with. These tools have adjustable settings that allow you to remove the insulation without damaging the wire. Avoid using a knife or pliers to strip wires, as this can easily lead to nicks or cuts. If you're using a wire stripper, make sure to squeeze the handles firmly and pull the insulation straight off the wire. Avoid twisting or yanking the wire, as this can also damage it.
After stripping the wire, inspect it carefully for any nicks or cuts. If you find any damage, cut off the damaged section and strip the wire again. It's better to lose a little bit of wire than to risk a weak or unreliable connection. Also, make sure to strip enough insulation off the wire to allow for a proper connection with the splicing method you're using.
Stripping wires correctly is a simple but vital skill. Taking the time to do it right ensures that your splice has the best possible start, setting the foundation for a safe, durable electrical connection. This may seem obvious, but it's something even professionals sometimes rush!
9. Secure Connections
A secure connection is the heart of a good wire splice. Whether you're using wire connectors, crimp connectors, or soldering, it's essential to ensure that the wires are tightly and securely connected. A loose connection can lead to resistance, heat, and eventual failure.
When using wire connectors, make sure to twist the wires together tightly before screwing on the connector. Also, make sure to use the right size of connector for the number and gauge of wires you're connecting. Overstuffing the connector can lead to a loose connection. When using crimp connectors, make sure to use the correct crimping tool and crimp the connector down tightly. A loose crimp can be just as bad as a loose wire nut connection.
If you're soldering wires, make sure to heat the wires properly and apply enough solder to create a strong bond. A cold solder joint (one that hasn't been heated enough) can be weak and unreliable. After making the connection, give the wires a gentle tug to make sure they're secure. If they pull apart easily, the connection isn't secure enough and needs to be redone.
Always give the wires a gentle tug test to make sure they are secure. This practice, though simple, can reveal potential issues before they become problems down the line.
10. Proper Insulation
Proper insulation is essential for preventing short circuits and protecting you from electrical shock. After making the electrical connection, you need to insulate the bare wires with an insulating material, such as electrical tape or heat-shrink tubing.
When using electrical tape, wrap the tape tightly around the wires, overlapping each layer to create a solid and waterproof seal. Use multiple layers of tape for added protection. When using heat-shrink tubing, slide the tubing over the wires before making the connection. After making the connection, use a heat gun or hair dryer to shrink the tubing around the wires, creating a tight and secure insulation.
Make sure that all of the bare wires are completely covered with insulation. Any exposed wire can pose a safety hazard. Also, make sure to use a high-quality insulating material that's designed for electrical applications. Avoid using duct tape or other non-electrical tapes, as these are not designed to provide adequate insulation.
In conclusion, applying the correct insulation is as important as the splice itself! When applying insulation, don't skimp on quality or coverage. It's the final safeguard that protects you and ensures the longevity of your electrical work. It's always wise to use the right material for insulation to the wires for future safety purpose.

FAQ
11. Q
A: Yes, you can, but it requires careful consideration. Using crimp connectors is generally the easiest and most reliable way to do this, but ensure the connector is rated for the specific gauge combination. When using wire nuts, it's crucial to pre-twist the wires tightly to ensure a solid connection. Soldering is also an option, but it requires more skill to execute safely and effectively.
12. Q
A: Yes, but you must use waterproof connectors or protect the connections with heat-shrink tubing. Water and electricity don't mix, so it's crucial to prevent moisture from entering the splice. Look for connectors specifically designed for outdoor use, which often include a sealant to prevent water ingress. Always prioritize safety and use the appropriate materials for the environment.
13. Q
A: Wire connectors (wire nuts) are generally the preferred method for splicing wires in a junction box. They're easy to use, relatively inexpensive, and provide a secure and insulated connection. Make sure the junction box is properly sized for the number of wires you're splicing, and never overfill it. Always follow local electrical codes and regulations.
14. Q
A: If you're not comfortable working with electricity, it's always best to call a qualified electrician. Electricity can be dangerous, and it's better to be safe than sorry. An electrician has the knowledge, skills, and experience to safely and effectively splice wires, ensuring that your electrical system is working properly and safely.
