Build A Info About What Are The Benefits Of Closed Loop Production
![Closedloop Production System [50]. Download Scientific Diagram Closedloop Production System [50]. Download Scientific Diagram](https://www.researchgate.net/publication/313291665/figure/fig1/AS:485536277241857@1492772277987/Closed-loop-production-system-50.png)
Closedloop Production System [50]. Download Scientific Diagram
Unlocking Efficiency
1. Understanding the Fundamentals
Ever wondered how some companies seem to just get it when it comes to minimizing waste and maximizing resources? Chances are, they're employing a strategy called closed loop production. The term itself might sound a bit technical, but the concept is actually quite straightforward: it's about designing your production processes so that waste materials are reintegrated back into the system, either as raw materials for the same product or for something entirely new. Think of it like a really efficient recycling system, but built directly into the manufacturing process. Forget linear we're talking cyclical!
Instead of the traditional "take-make-dispose" model, closed loop production aims for a more sustainable and resource-conscious approach. Imagine a brewery that collects spent grain and uses it to create animal feed. Or a clothing manufacturer that recycles fabric scraps into new garments. That's the essence of the closed loop system in action. It's about thinking beyond the initial product and considering the entire life cycle of materials.—from sourcing to disposal or, more accurately, repurposing.
The core of this system is the word 'closed'. Closed loop production is all about creating a circular economy where waste is minimized, and resources are utilized to their fullest potential. It's a shift from viewing waste as an inevitable byproduct to seeing it as a valuable resource waiting to be unlocked. A key aspect is identifying potential waste streams within your production process. What materials are being discarded? Could these be reused, repurposed, or recycled in some way?
This is achieved by designing products and processes with end-of-life considerations in mind. The goal is to minimize waste and maximize the value of materials by reusing, repairing, refurbishing, or recycling them. This approach reduces reliance on virgin resources, lowers environmental impact, and can even create new business opportunities. The noun "production" serves as the main point, as this is where the actions take place and what we aim to benefit from in a closed loop.
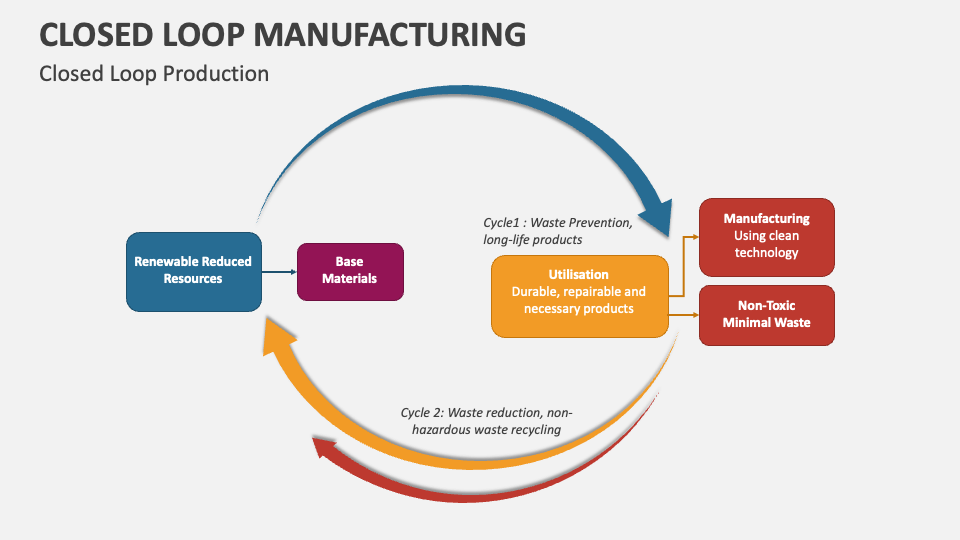
Closed Loop Manufacturing PowerPoint Presentation Slides PPT Template
The Perks
2. Exploring the Advantages
Alright, let's get to the good stuff! Why should a company even bother with closed loop production? Well, the benefits are numerous and far-reaching. First and foremost, it's a fantastic way to reduce waste. By reintegrating materials back into the production cycle, you significantly decrease the amount of waste that ends up in landfills. Think of the planet! And the positive PR! Less waste, happier planet, happier customers. It's a win-win-win, really.
Another major advantage is the cost savings. By using recycled or repurposed materials, you can reduce your reliance on expensive virgin resources. Plus, you might even be able to generate revenue by selling your waste materials to other companies. So, it's not just about cutting costs; it's about creating new revenue streams. Who wouldn't want that?
Beyond the financial benefits, closed loop production can also improve your company's brand image. Consumers are increasingly concerned about sustainability, and they're more likely to support companies that are committed to environmentally responsible practices. By embracing closed loop production, you can demonstrate your commitment to sustainability and attract environmentally conscious customers. Consider it as a significant marketing advantage.
Finally, it enhances supply chain resilience. By diversifying resource streams and reducing dependence on volatile primary materials, companies can better withstand disruptions and uncertainties. This approach fosters innovation by encouraging companies to develop new products and processes that align with circular economy principles. Overall, closed-loop production not only benefits the environment and society but also creates tangible business value and enhances long-term sustainability.
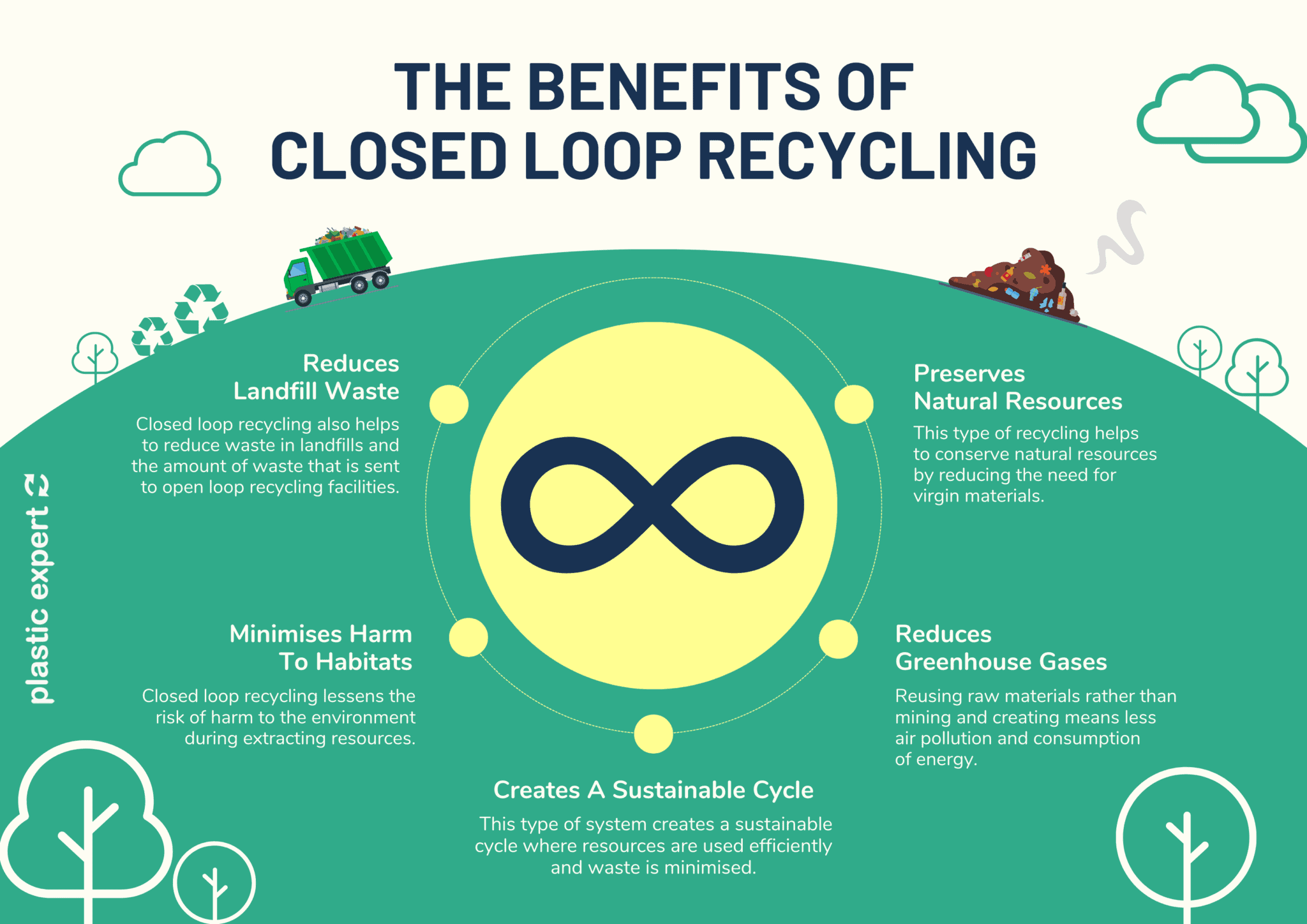
What Is Closed Loop Recycling Plastic Expert
Getting Started
3. Practical Steps for Adoption
So, you're convinced. Closed loop production sounds amazing, but how do you actually implement it? Start by conducting a thorough assessment of your current production processes. Identify the areas where waste is generated and determine the potential for reusing, repurposing, or recycling those materials. Think of it like a treasure hunt, but instead of gold, you're looking for waste streams!
Next, explore potential partnerships with other companies. Maybe your waste materials could be used as raw materials for another manufacturer. Or maybe you could collaborate on developing new products that are designed for recyclability. Collaboration is key to making closed loop production a success. Building a network of partners and stakeholders is essential.
Don't forget about product design! Designing products with end-of-life considerations in mind is crucial for closed loop production. Use materials that are easy to recycle or repurpose, and design products that can be easily disassembled and repaired. Consider modular designs that allow for easy component replacement and upgrades. If its easy to dismantle, it is easy to reuse.
Furthermore, it is vital to prioritize transparency and traceability in your supply chain to ensure the integrity of recycled materials. Communicate your closed-loop initiatives to customers and stakeholders to build trust and enhance brand reputation. Continuously monitor and evaluate your closed-loop processes to identify areas for improvement and optimization.

Closed Loop Production Systems (adapted Upon OECD, 2009) Download
Overcoming the Hurdles
4. Navigating Potential Roadblocks
Okay, let's be realistic. Implementing closed loop production isn't always a walk in the park. There can be challenges, such as the cost of investing in new equipment or processes. Or the difficulty of finding reliable sources of recycled materials. It requires careful planning and investment.
Another challenge is ensuring the quality of recycled materials. You need to make sure that the materials you're using meet your quality standards and won't compromise the performance of your products. Quality control is a critical aspect of successful closed loop production. Invest in rigorous testing and inspection processes to ensure consistency.
Sometimes, regulations can also be a barrier. Some regulations may not be designed to accommodate closed loop production, which can make it difficult to get the necessary permits or approvals. Stay informed about relevant environmental regulations and advocate for policies that support circular economy initiatives. Engaging with regulatory bodies can help shape a more conducive environment for closed loop production.
However, these challenges can be overcome with careful planning, innovation, and collaboration. By addressing these potential roadblocks head-on, you can successfully implement closed loop production and reap the many benefits it offers. The most important thing to remember is that you are contributing towards creating a sustainable environment.
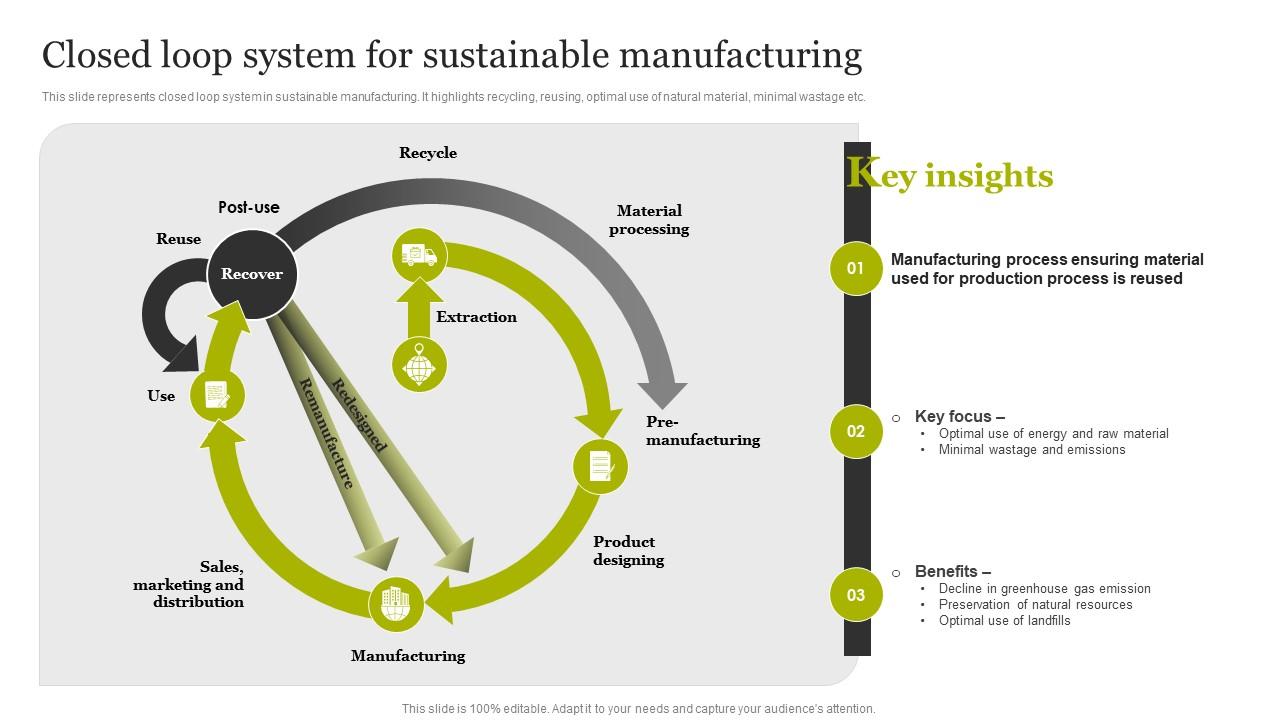
The Future is Circular
5. Looking Ahead
Closed loop production isn't just a trend; it's the future of manufacturing. As resources become more scarce and environmental concerns continue to grow, companies will increasingly need to embrace closed loop strategies to remain competitive and sustainable. Those who embrace this paradigm shift will be better positioned for long-term success.
We're already seeing a growing number of companies adopting closed loop practices, from fashion brands that recycle textiles to electronics manufacturers that take back old devices for recycling. This trend is only going to accelerate in the years to come. These companies are paving the way for a more sustainable future.
So, whether you're a small business owner or a large corporation, now is the time to start exploring the possibilities of closed loop production. By embracing this new paradigm, you can reduce waste, save money, improve your brand image, and contribute to a more sustainable future for all. By investing in closed-loop production, your contributing towards a better future for the world.
The journey towards circularity requires a commitment to innovation, collaboration, and continuous improvement. As technology advances and consumer awareness grows, closed-loop production will become even more efficient and effective. Embrace the change and join the movement towards a circular economy.

Closed Loop Manufacturing Explained Sustainability Ford YouTube
FAQs About Closed Loop Production
6. Your Burning Questions Answered
Still have some questions swirling around in your head? No problem! Here are a few frequently asked questions to help clarify things:
7. What's the difference between closed loop production and recycling?
Recycling is often an end-of-life process, where materials are collected and processed after they've been used. Closed loop production integrates recycling directly into the manufacturing process, so waste materials are immediately reused or repurposed. Think of it as proactive vs. reactive.
8. Is closed loop production only for large companies?
Absolutely not! While large companies may have more resources to invest in closed loop initiatives, even small businesses can implement closed loop strategies. Simple things like reusing packaging materials or donating scrap materials to local artists can make a big difference. Its about being resourceful and creative!
9. How do I measure the success of my closed loop production efforts?
You can track key metrics such as the amount of waste diverted from landfills, the reduction in virgin material usage, the cost savings achieved, and the improvement in your brand reputation. Regular monitoring and reporting are crucial for assessing progress. Also, don't forget about the positive environmental impact!