Ideal Info About How To Troubleshoot An Inductor
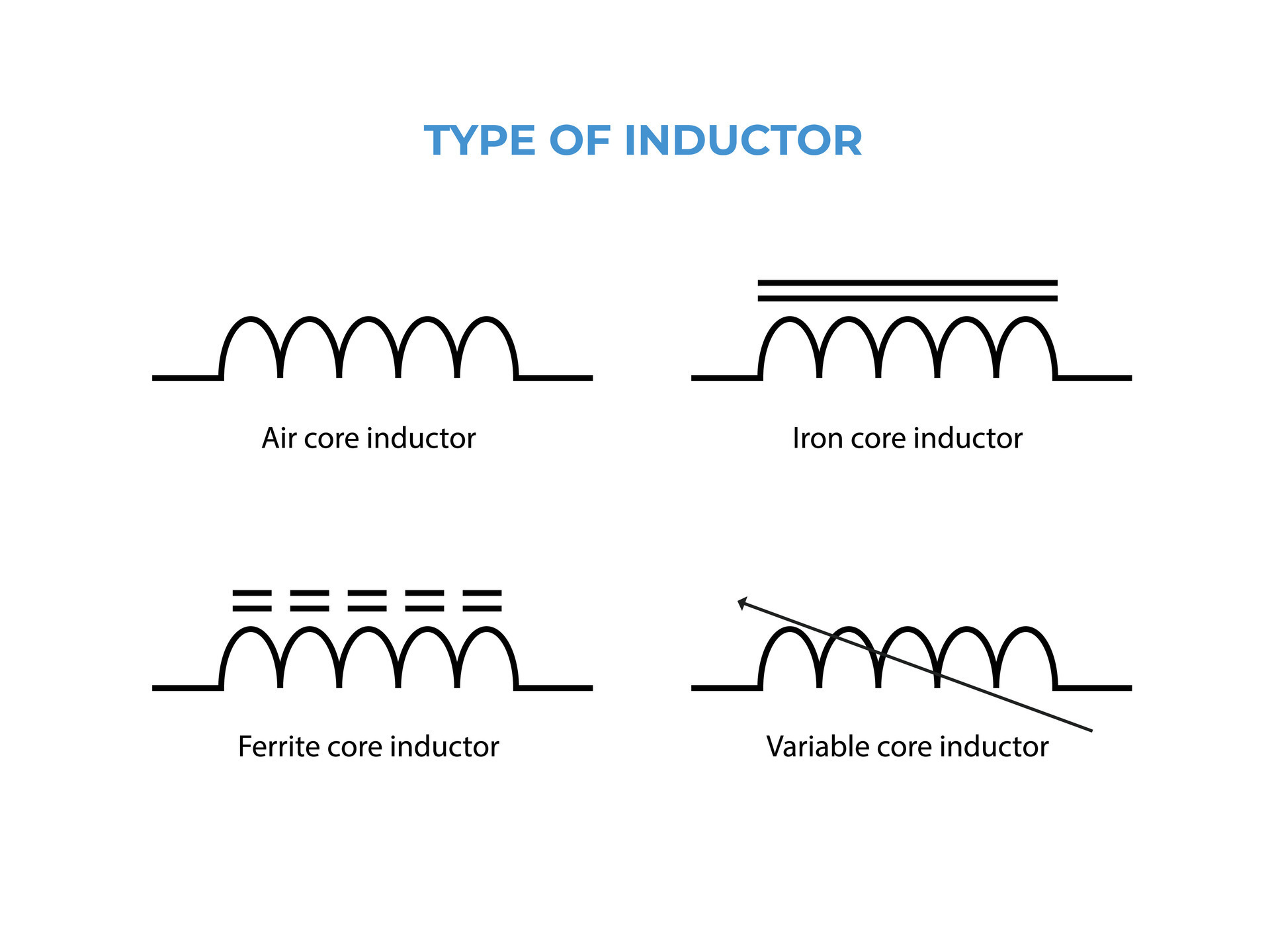
Iron Core Inductor Schematic Symbol Symbo
Troubleshooting Inductors
1. Understanding the Basics Before You Start
So, you're having inductor issues? Don't sweat it! Inductors, while seemingly simple, can sometimes throw a wrench into your circuits. Let's approach this methodically. Before diving into troubleshooting, it's good to have a basic understanding of what an inductor actually does. Think of it like a tiny electrical reservoir. It stores energy in a magnetic field when current flows through it, and then releases that energy when the current changes. They're vital for filtering, energy storage, and all sorts of cool applications.
What makes an inductor tick? Its inductance value (measured in Henries) is the key. This tells you how much magnetic field it creates for a given current. Factors like the number of coil turns, the core material, and the physical size all influence the inductance. A bigger coil with more turns generally means a higher inductance. And if the inductor has a core material, like iron, this can also boost the inductance significantly.
Now, let's talk about what can go wrong. Common inductor ailments include open circuits (broken connection), shorted turns (insulation failure within the coil), and changes in inductance value. These problems can manifest as circuit malfunctions, overheating, or even complete failure of a device. A faulty inductor can mimic other problems in a circuit, making diagnostics tricky.
Therefore, familiarizing yourself with the inductors role in the specific circuit youre working on is crucial before you even reach for your multimeter. Refer to the circuit diagram, understand the intended frequency response, and note any expected voltage or current levels. This will give you a baseline for comparison and make identifying anomalies much easier. So, armed with this basic knowledge, let's get ready to troubleshoot!
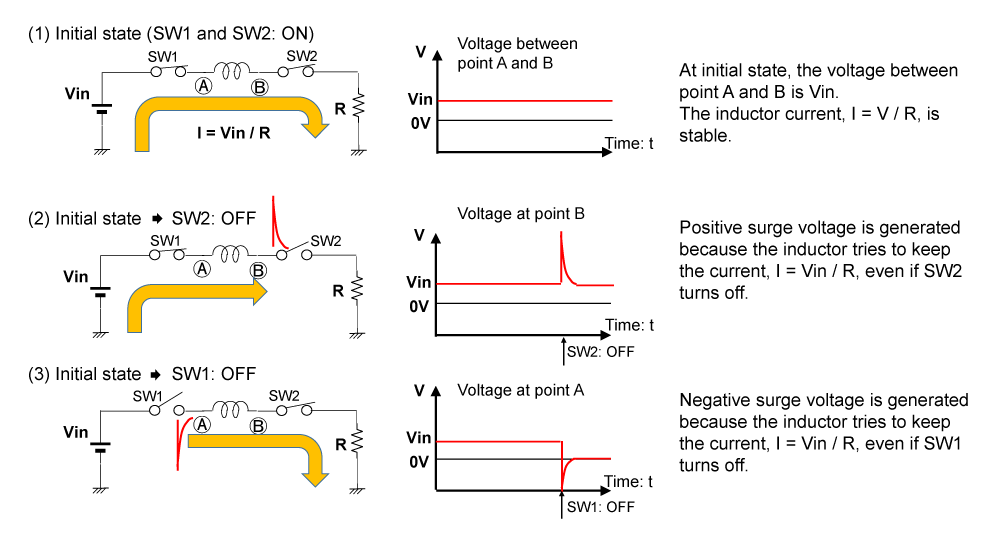
What Is A DC/DC Converter? Part 3 Design Supports Nisshinbo Micro
Gathering Your Tools and Safety First
2. Essential Equipment and Precautions
Okay, time to assemble the toolbox. You'll need a few key items: a multimeter (the Swiss Army knife of electronics!), a soldering iron (if you suspect connection issues), and maybe an LCR meter (for precise inductance measurement, though not always essential). A good set of alligator clips can also be incredibly helpful for temporary connections.
Safety is paramount, my friend! Always disconnect the power supply before working on any circuit. Capacitors can hold a charge even after the power is removed, so discharge them carefully using a resistor. Wear appropriate safety glasses to protect your eyes, and if youre soldering, ensure you have adequate ventilation to avoid inhaling fumes.
Before you even start probing around, take a good look at the inductor itself. Are there any visible signs of damage? Burn marks, cracked casing, or loose wires are all red flags. If you see something that looks suspicious, that inductor is probably the culprit. Also, give the inductor a gentle wiggle. If it feels loose on the board, the solder joints may be compromised.
Remember, working with electronics involves potential hazards. Approach the task with a clear head, take your time, and never rush. If you're unsure about something, consult a qualified technician. After all, it's better to be safe than sorry (and potentially electrocuted!).
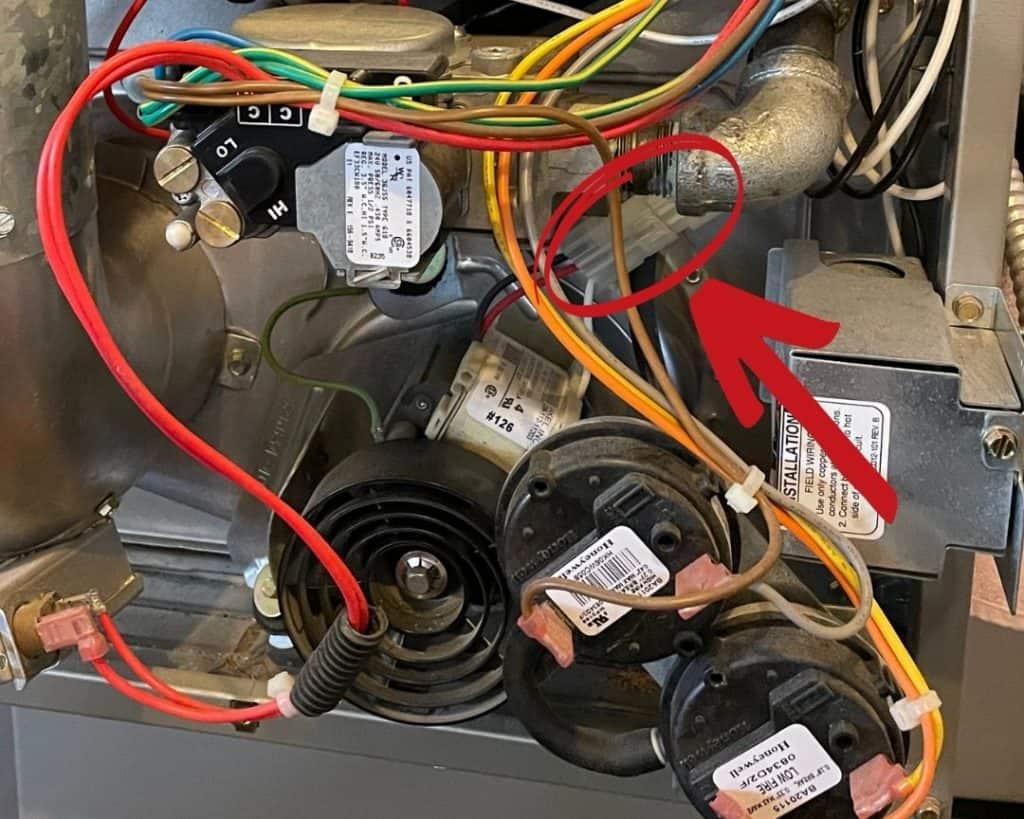
Furnace Inducer Troubleshooting Here’s What To Do HVAC Training Shop
Basic Inductor Testing with a Multimeter
3. Checking for Opens and Shorts
The multimeter is your first line of defense. Set it to the resistance (Ohms) setting. We're primarily looking for two things: an open circuit (infinite resistance) or a short circuit (very low resistance). An open circuit means the inductor coil is broken, while a short circuit indicates a fault within the coil's windings.
Touch the multimeter probes to the inductor's terminals. A healthy inductor should show a low resistance, usually a few Ohms, depending on its size and construction. An open circuit (indicated by an "OL" or infinite resistance reading) means the inductor is definitely toast. A very low resistance (close to zero) suggests a shorted turn within the coil, which is equally bad.
Sometimes, the resistance reading might be slightly higher than expected. This could be due to the internal resistance of the multimeter itself, or the leads. To compensate, short the multimeter leads together and note the reading. Subtract this value from your inductor measurement to get a more accurate result. This is particularly important for low-value inductors.
Bear in mind that this test only gives you a basic pass/fail indication. It won't tell you if the inductance value is correct or if the inductor is performing optimally under different frequencies. For more in-depth analysis, you'll need an LCR meter, which we'll discuss later. But for a quick and dirty check, the multimeter is your friend.

Advanced Inductor Testing with an LCR Meter
4. Measuring Inductance and Other Parameters
If your multimeter check didnt reveal any obvious faults, but you still suspect the inductor is causing problems, it's time to bring out the big guns: the LCR meter. This device is designed to accurately measure inductance (L), capacitance (C), and resistance (R) at various frequencies.
Connect the inductor to the LCR meter's terminals. Select the appropriate measurement frequency (typically 1 kHz or 10 kHz, depending on the inductor's intended application). The meter will display the inductance value. Compare this value to the inductor's specified inductance. A significant deviation (usually more than 10%) indicates a problem.
But wait, there's more! LCR meters can also measure other important parameters like the quality factor (Q) and the dissipation factor (D). The Q factor indicates the inductor's efficiency — how well it stores energy compared to how much energy it dissipates as heat. A high Q factor is generally desirable. The dissipation factor (D) is the inverse of Q, and a low D factor is preferable.
Pay attention to the LCR meter's readings at different frequencies. An inductor's performance can vary significantly with frequency. If the inductance value or Q factor drops dramatically at a particular frequency, it could indicate resonance issues or core losses. This can be particularly important in high-frequency applications. An LCR meter is a very useful tool, but keep in mind some cost more than other testers.

Inductors Repair Basics Wiki
Checking for External Factors and Environmental Influences
5. Temperature, Connections, and Component Proximity
Sometimes, the inductor itself isn't the problem. External factors can also affect its performance. Temperature, for example, can influence inductance values, especially in inductors with ferrite cores. High temperatures can cause the core material to lose its magnetic properties, leading to a decrease in inductance.
Poor connections are another common culprit. A corroded or loose solder joint can introduce unwanted resistance into the circuit, affecting the inductor's performance. Carefully inspect the solder joints around the inductor. If they look dull or cracked, reflow them with a soldering iron.
Component proximity can also play a role. If the inductor is located too close to other components, especially transformers or other inductors, electromagnetic interference can occur. This can distort the inductor's magnetic field and affect its performance. Try moving the inductor away from other components or shielding it with a metal enclosure.
Don't underestimate the importance of a visual inspection. Look for signs of corrosion, moisture, or physical damage to surrounding components. A seemingly unrelated problem nearby can sometimes manifest as an inductor issue. This sort of thing is often overlooked, but it's often a key factor that can save you hours of frustration!
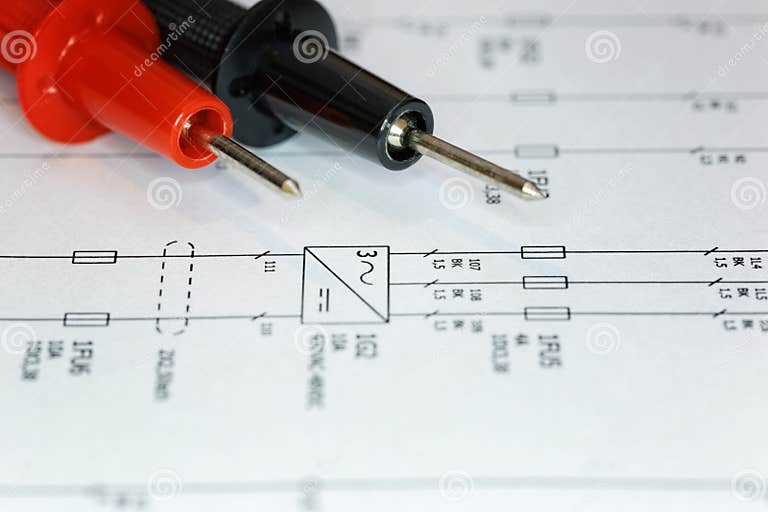
Electrical Chart, Troubleshoot. Stock Photo Image Of Inductor
When to Replace the Inductor
6. Recognizing Irreversible Damage
Okay, you've done your troubleshooting, and the inductor is clearly faulty. When is it time to throw in the towel and replace it? If the inductor shows an open circuit, a short circuit, or a significant deviation in inductance value (beyond the manufacturer's tolerance), replacement is usually the best option.
Visible damage is another clear indicator. If the inductor has a cracked core, burnt casing, or loose windings, it's unlikely to perform reliably, even if it still shows a reasonable inductance value. These kinds of damages usually signal future issues.
Sometimes, the inductor might appear to be working fine, but it's causing intermittent problems in the circuit. This can be tricky to diagnose. If you've ruled out other potential causes and you still suspect the inductor, consider replacing it as a preventative measure, especially if it's a critical component.
When replacing the inductor, make sure to use a component with the same specifications: inductance value, current rating, and physical size. Using an incorrect inductor can cause further damage to the circuit. Take the time to look up the original part number and order a suitable replacement. After all, the goal here is to fix your circuit, not make things worse!