Fine Beautiful Info About How Many Types Of Motor Controllers Are There
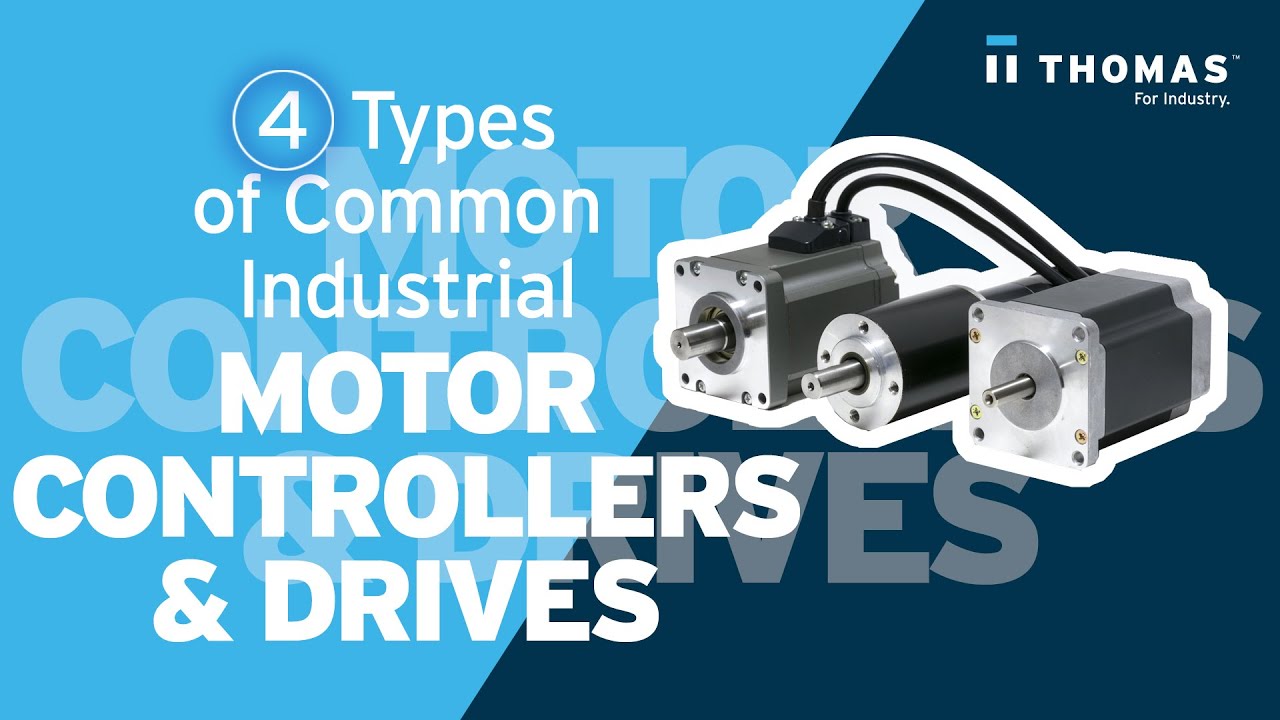
Decoding the Mystery
1. Understanding the Basics of Motor Control
So, you're curious about motor controllers? Excellent! Think of them as the brains behind the brawn of electric motors. Without them, motors would just spin wildly out of control, kind of like my attempts at making sourdough bread. Motor controllers regulate a motor's performance, ensuring it starts, stops, accelerates, decelerates, and generally behaves itself according to the task at hand. Essentially, they prevent your motor from having an existential crisis and burning itself out. The keyword here is "motor controllers", which, in this context, are nouns.
Different applications demand different levels of sophistication. Imagine trying to drive a golf cart with the same controller you use for a tiny electric fan. Catastrophe! That's why we have such a variety of motor controllers. Its not just about turning things on and off; it's about precision, efficiency, and safety. So, let's dive into this fascinating world of managing those electric beasts.
The world of motor controllers is surprisingly vast and diverse. It's not a one-size-fits-all situation. From the simplest on/off switch to complex, programmable systems, each type has its own strengths and weaknesses. Picking the right one is crucial for optimizing performance, extending motor life, and preventing potential disasters. Trust me, you don't want your motor to stage a revolt.
Consider the environment the motor is operating in. Is it a delicate laboratory setting requiring smooth, precise movements? Or is it a rugged industrial application demanding high torque and durability? These factors heavily influence the type of motor controller you'll need. Think of it like choosing the right tool for the job; a screwdriver wont hammer a nail, and a basic controller wont manage a complex motor system.

The Simplicity of On/Off Starters
2. The Reliable Workhorse
Let's start with the basics: On/Off starters. These are the simplest type of motor controller, and they do exactly what they say on the tin — they start and stop the motor. Think of them as the light switches of the motor world. Theyre robust, reliable, and ideal for applications where precise control isn't required, like simple pumps or fans. They are typically used to provide overload protection, which is really great.
While straightforward, On/Off starters can be quite hard on motors. They subject the motor to a sudden inrush of current during startup, which can cause stress and reduce its lifespan. It's like going from zero to sixty in a split second — exciting, but not sustainable. That said, for less demanding applications where cost is a major factor, they remain a viable option.
Despite their simplicity, these starters often incorporate protective features like overload relays and fuses. These safeguards prevent the motor from overheating or sustaining damage due to excessive current draw. It's like having a built-in insurance policy for your motor, protecting it from unforeseen electrical hazards.
Think of your everyday appliances — many use basic on/off starters. While more advanced options exist, the sheer simplicity and low cost of these starters make them suitable for a wide variety of applications. They might not be glamorous, but they are dependable and essential in countless scenarios.
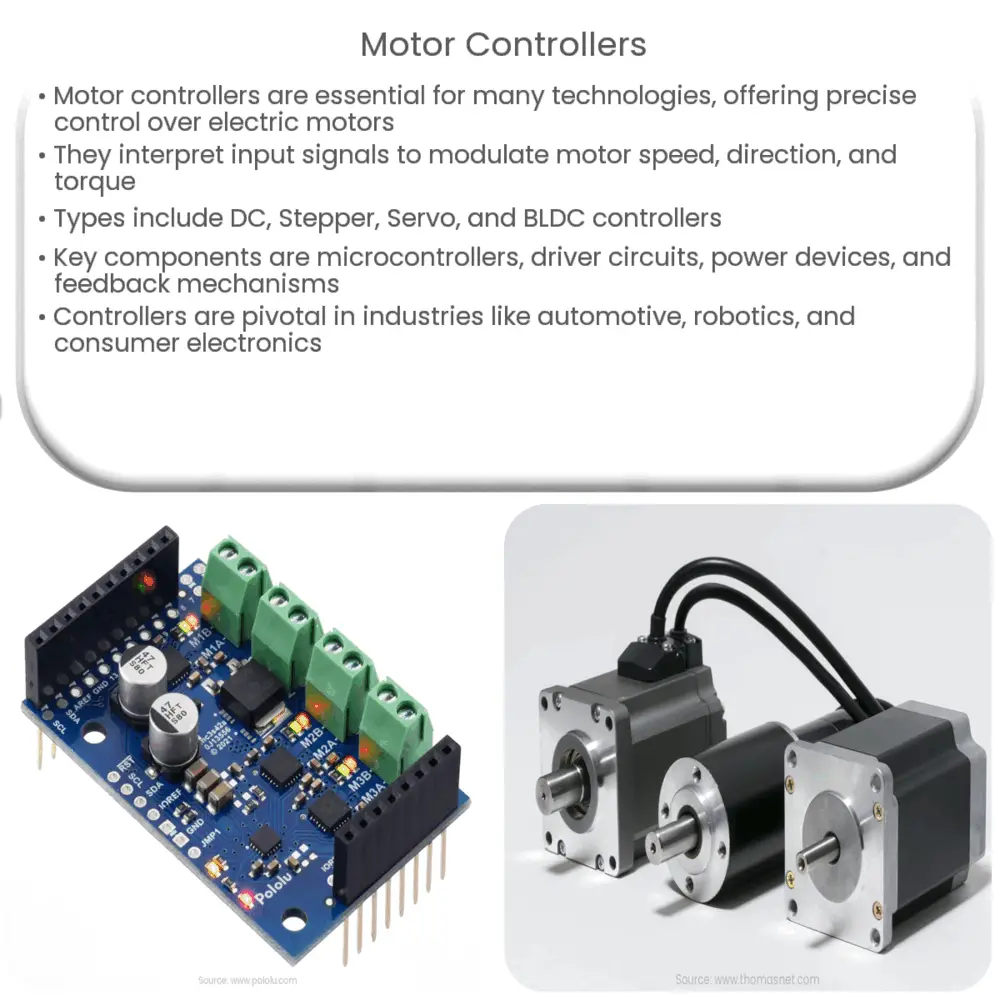
Motor Controllers How It Works, Application & Advantages
Stepping Up the Game
3. Easing the Strain on Your Motor
Next up, we have reduced voltage starters. These controllers are designed to mitigate the stress caused by the high inrush current of a direct On/Off start. Imagine gently easing into your morning routine instead of leaping out of bed and into a cold shower. Reduced voltage starters do the same thing for motors, providing a more gradual start. They come in several varieties, including autotransformer starters, part-winding starters, and resistance starters.
Autotransformer starters use a transformer to reduce the voltage applied to the motor during startup, gradually increasing it as the motor speeds up. Part-winding starters engage only a portion of the motor windings during startup, reducing the initial current draw. Resistance starters insert resistors in series with the motor windings to limit the current, gradually removing them as the motor accelerates. Each method has its pros and cons, depending on the specific application and motor characteristics.
These starters are particularly useful for larger motors that would otherwise draw excessive current during startup, potentially causing voltage dips and disruptions to the power grid. Think of them as responsible citizens, preventing electrical chaos and ensuring a smooth power flow for everyone.
While more complex and expensive than On/Off starters, reduced voltage starters offer significant benefits in terms of motor longevity and electrical system stability. They represent a sweet spot between simplicity and sophistication, providing a balance of performance and cost-effectiveness for many applications.
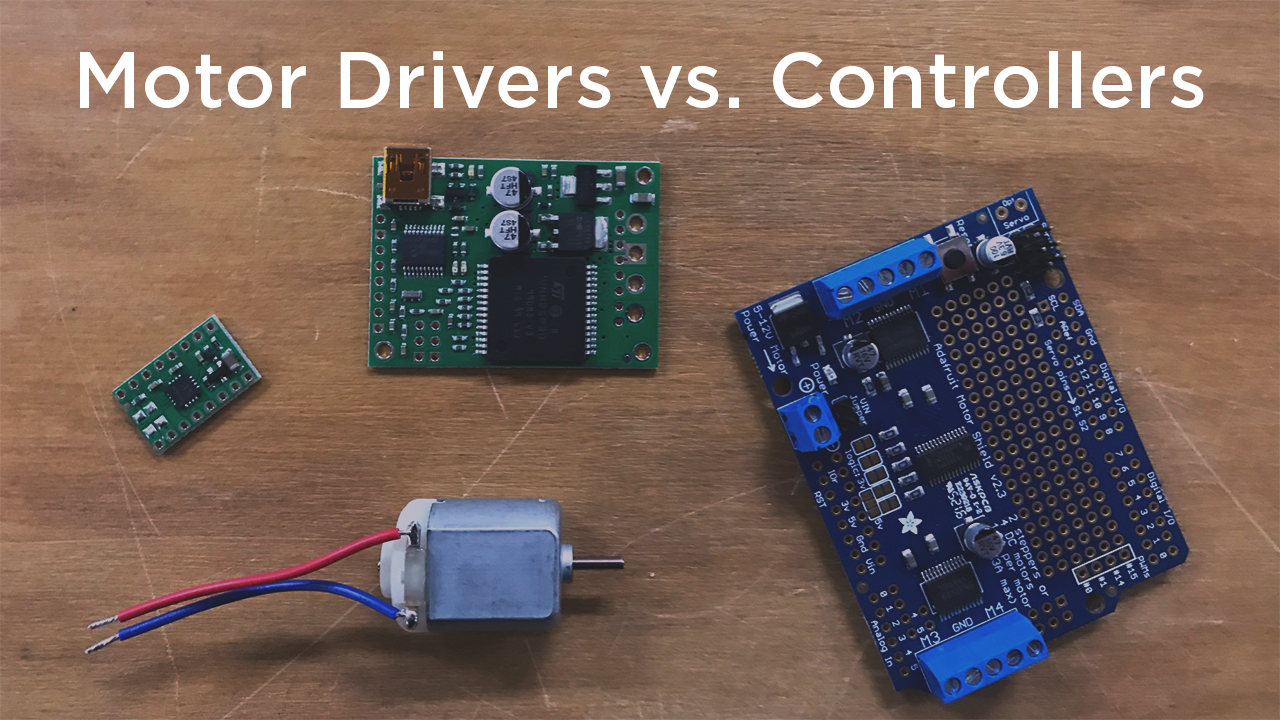
Motor Drivers Vs. Controllers Tutorial Australia
The Sophistication of Variable Frequency Drives (VFDs)
4. The Masters of Motor Control
Now we're getting into the really interesting stuff: Variable Frequency Drives (VFDs). These are the rock stars of motor control, offering unparalleled flexibility and precision. VFDs control the motor's speed by varying the frequency of the power supplied to it. This allows for smooth acceleration and deceleration, precise speed control, and significant energy savings.
Imagine having a volume knob for your motor's speed — that's essentially what a VFD provides. They're used in a wide range of applications, from controlling the speed of conveyor belts in factories to regulating the flow of water in pumps. They can also be programmed to perform complex tasks and integrate with other control systems, making them incredibly versatile. They are super efficient and safe in the industry.
VFDs are also great for energy efficiency. By optimizing the motor's speed to match the load requirements, they can significantly reduce energy consumption. Think of it as driving your car at the optimal speed for fuel economy — you're not wasting energy unnecessarily. This can lead to substantial cost savings over time, making VFDs a worthwhile investment.
However, VFDs are more complex and expensive than other types of motor controllers. They also require careful installation and programming to ensure optimal performance. But for applications that demand precise control, energy efficiency, and advanced features, VFDs are the clear choice. They truly represent the pinnacle of motor control technology.
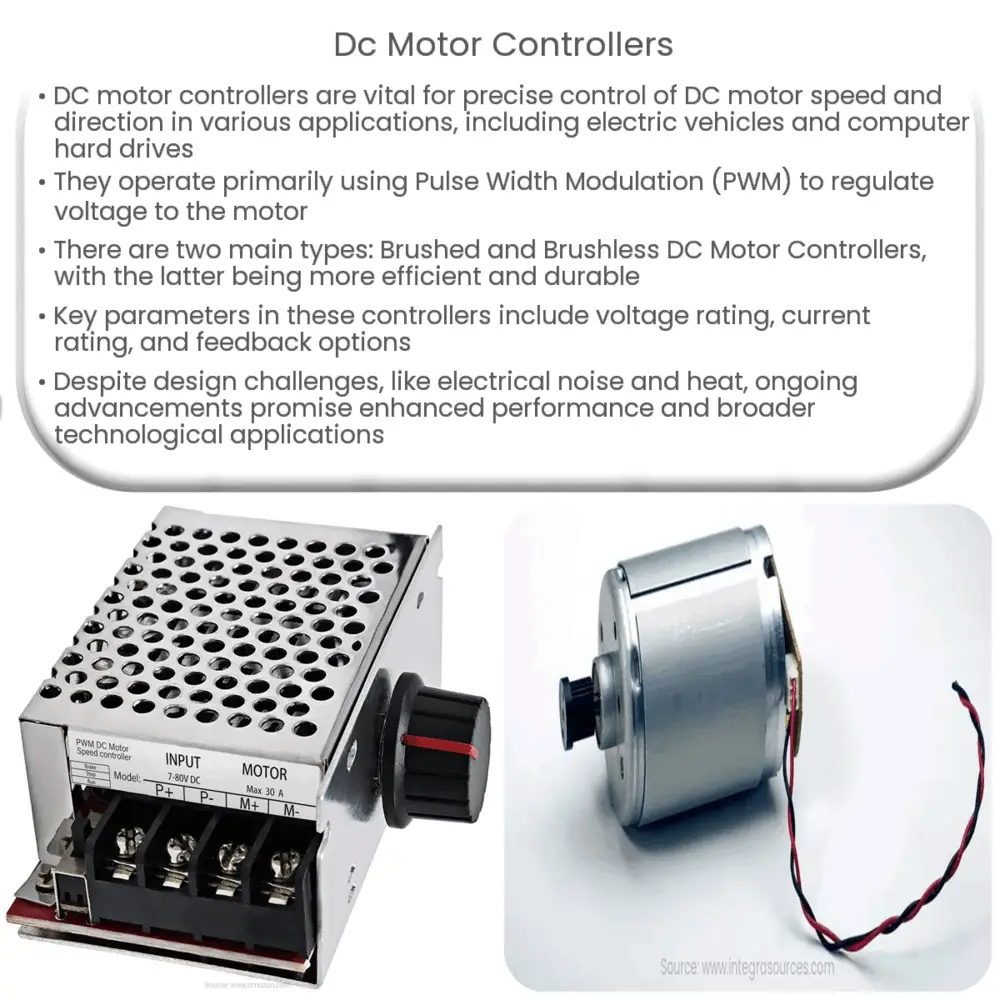
Motor Controllers How It Works, Application & Advantages
Servo Drives and Stepper Motor Controllers
5. The Microscopic Masters
For applications demanding extreme precision, such as robotics and CNC machines, servo drives and stepper motor controllers are the go-to options. These controllers provide precise control over the motor's position and speed, allowing for incredibly accurate movements. Servo drives use feedback from encoders to continuously adjust the motor's position, ensuring it stays exactly where it needs to be. Stepper motor controllers, on the other hand, divide the motor's rotation into discrete steps, allowing for precise incremental movements.
Imagine controlling a robotic arm with pinpoint accuracy or carving intricate designs with a CNC machine. These applications require a level of precision that only servo drives and stepper motor controllers can provide. They're the unsung heroes of the automation world, enabling complex and delicate tasks to be performed with ease and accuracy.
These controllers are typically more expensive and complex than other types, but their precision capabilities are unmatched. They require careful tuning and configuration to achieve optimal performance, but the results are well worth the effort for applications demanding absolute accuracy.
Think of the precision required in medical devices or scientific instruments. Servo drives and stepper motor controllers play a critical role in these applications, ensuring accurate and reliable performance. They are the pinnacle of precision motor control, enabling advancements in various fields.
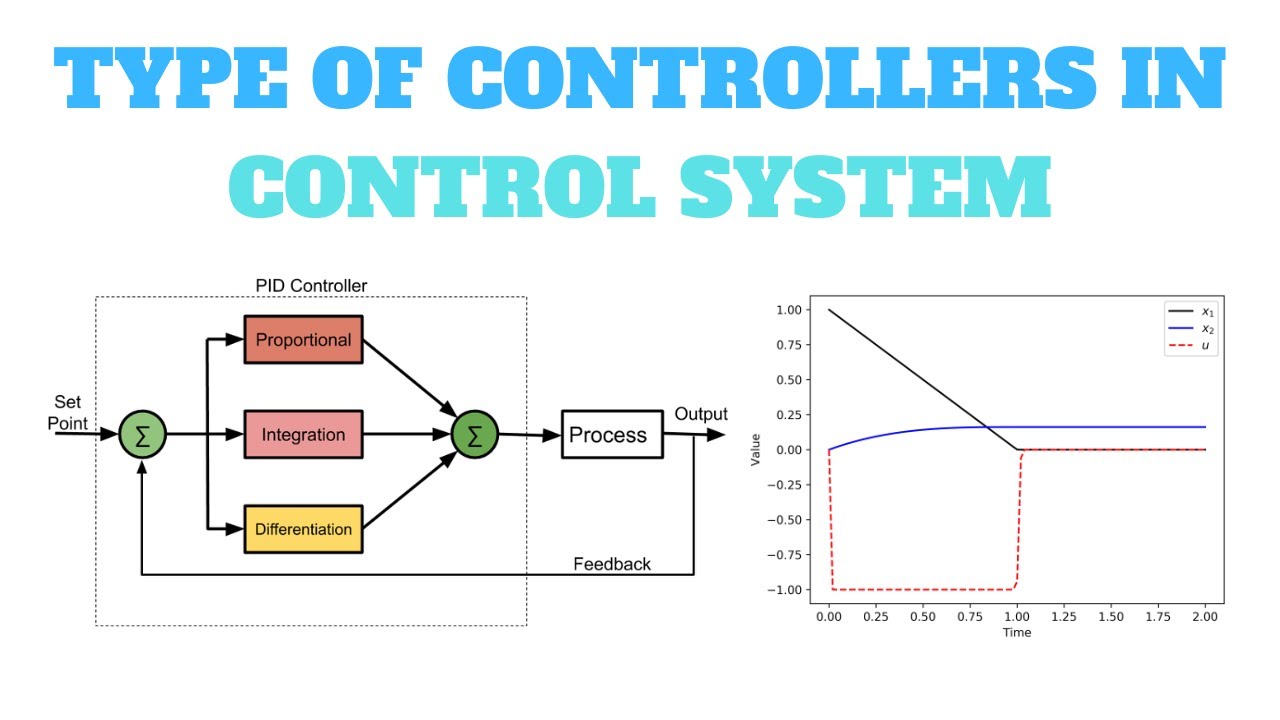
Type Of Controllers In Control System YouTube
Other Notable Types
6. Rounding Out the Roster
While we've covered the main categories, it's worth mentioning a few other notable types of motor controllers. Soft starters, for instance, are similar to reduced voltage starters but offer even smoother and more controlled starts. They're often used in applications where minimizing mechanical stress on the motor and driven equipment is crucial. Think of them as the gentle giants of motor control, providing a smooth and cushioned start.
DC motor controllers are specifically designed for controlling DC motors, which have different characteristics than AC motors. These controllers often use pulse-width modulation (PWM) to control the motor's speed and torque. They are a staple in industries, and are super effective in providing motor control.
Intelligent motor controllers (IMCs) integrate advanced features like diagnostics, communication capabilities, and programmable logic. They can monitor motor performance, detect faults, and communicate with other control systems. They're the smart kids of the motor control world, offering a wealth of information and control options.
The world of motor controllers is constantly evolving, with new technologies and innovations emerging all the time. Staying up-to-date with the latest advancements is crucial for selecting the optimal motor controller for your specific application. Remember, the right controller can make all the difference in terms of performance, efficiency, and reliability.